Frequently Asked Questions
Oil Pumps
Pump cavitation is the rapid creation and collapse of air bubbles in the oil. These bubbles are created by rapid changes in pressure inside the pump. When these bubbles collapse, shock waves are created. These repeated shock waves will erode or create pits on the pump components, this results in reduced pump efficiency and premature wear on components and in extreme cases pump failure. Most common causes of cavitation include undersized lines or fittings, numerous bends and fittings, excessive pump speed, leaks that allow air into an oil line, and an oversized or undersized pump for the application. Poor drain back and scavenging can also cause these symptoms as the oil tank will no longer have a tall column of oil over the pickup tube.
No, you cannot create crankcase vacuum with a single stage oil pump. Peterson manufactures a Wet-Vac™ oil pump which combines our wet sump oil pump with a vacuum pump from Star Machine for those who want to have crankcase vacuum in a wet sump application. If you are not using a vacuum pump in a wet sump engine, it is impossible to create crankcase vacuum.
Pump selection is based on a number of factors and what works good on one engine may not be the best choice for another. It is recommended to call Peterson and talk to a sales representative who can guide you thru the process to get you the correct pump. Typical questions that will be asked.
- 1. Block and rod material?
- 2. Is the engine naturally aspirated?
- 3. Rod and main bearing clearances?
- 4. What type of racing is the engine for?
- 5. What is the desired oil psi?
- 6. What weight oil will be run?
- 7. How many scavenge sections are needed?
- 8. If engine is boosted how much psi?
In modern racing engines, control of windage (oil in suspension inside the engine) is one of the best ways to gain usable power. Evacuation of the crankcase can be better accomplished using multiple scavenge sections. All Peterson Dry Sump pumps, along with our competitors, use one pressure and 2, 3, or 4 scavenge stages. We have found that the Peterson 4 stage pump is as efficient as most 5 stage gear pumps, because of Peterson's Gerotor design. Typically, 3 stage pumps scavenge with 2 pickup points in the pan, 4 stage scavenge with 2 pickup points in the pan and one pickup out of the lifter valley. 5 stage pumps scavenge with 3 pickup points in the pan and one pickup out of the lifter valley. Most pump manufacturers offer different size stages which pump more or less volume per rotation. Typically, the longer the section - the more volume
Pump draw rods are torqued to 80 in-lbs. After the first heat cycle of the pump, draw rods need to be checked for torque. Periodically, the draw rods should also be checked as normal maintenance on the car.
No, this can result in catastrophic engine failure. Most check valves will not fully open with vacuum and they may not open at all. This creates a restriction in flow which will cavitate the oil pump and starve the engine of oil. If the oil gravity drains to the pan spin the pump with a drill to circulate the oil back to the dry sump tank.
No, unless you are scavenging cylinder heads. Combining two scavenge lines from an oil pan will result in oil not being scavenged correctly from the engine.
NO! All stages of the pump need oil to operate properly and if a stage is capped off it will result in oil pump damage.
Dowel pins were in the R4 pump for fixturing of the pump bodies during manufacturing. We have changed that fixturing, so the dowel pins are no longer needed.
Maintenance on the rear drive of the oil pump will vary due to racing conditions. Typically, you should clean and regrease the rear hex drive every few races . Some applications that are in extremely harsh conditions should be cleaned and regreased after every race.
Most likely, the relief in the Peterson oil pump and the remote relief are working against each other. You will need to block off the relief in the oil pump to fix the issue. Use blockoff part number 13-2920 for R4 pumps. This blockoff rod will replace the internals on the relief section of the pump.
Drives
Peterson oil pumps are ideally set up to turn in the 4500-4800 rpm range for maximum efficiency. There are instances where the pump speed will be slower due to engine requirements. We manufacture many pulleys so we can achieve the correct ratio for your engine. Turning the pump faster that 5000 rpm could result in cavitation.
HTD (High Torque Drive) or Gilmer belts will both work for an external oil pump. HTD belts utilize a rounded tooth profile which distributes stress evenly across the pulley. This reduces noise and vibration compared to a Gilmer belt and there are more options for length, so they are typically the recommended style of belt. Gilmer belts use a square tooth profile. Peterson manufactures pulleys and belts in both styles.
Unlike v-belts or serpentine style belts, toothed belts like HTD and Gilmer do not need to be overly tight. The teeth on the belt are doing the work instead of friction. A good rule is that you should be able to turn the belt 90º and see the teeth on the belt. Do nto be alarmed if it appears that belt seems to be bouncing or flapping while the engine is running. If you over tighten these style belts they can walk off the pulley or cause premature wear to your pulleys.
Filters
Peterson filter elements are rated in micron sizes, the larger the micron size the larger the particle that will pass through the element. The proper element will filter any particle that is larger than the rod and main bearing clearances and allow enough flow for the grade of oil used. Multi-viscosity oils will typically use a 60 micron element and 70 weight oil will use a 75 to 100 micron element. Oil filters on the pressure side of the system should always have a bypass.
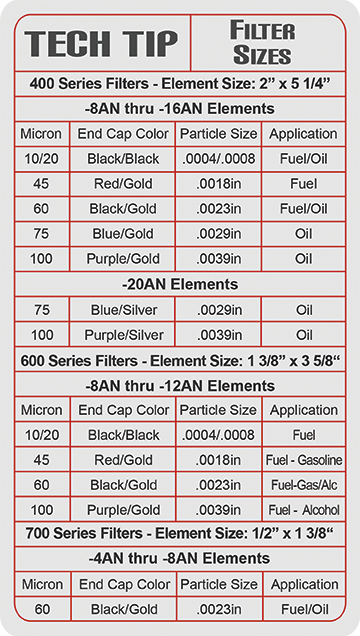
Oil Tanks
Peterson oil tanks are rated in system capacity, line size and length will affect how much oil is held in the system. When initially filling, add oil till 2/3 full and prime the system. Refill back to 2/3 full and start engine and with the engine operating at 3000 rpm oil tank should be between ½ and 2/3 full. If oil blows out the breather, lower tank level by a quart but never go below ½ full. To check tank level Peterson makes oil tank dipsticks for all standard tank sizes.
When plumbing in a breather can, to breath the engine, you should use at least a - 12 AN hose. The hose should run slightly up hill to the can so that any oil reaching the hose can run back down the hose to the tank. Be sure that the hose does not have any dips where oil can accumalate. Remember- The air coming from the oil tank to the breather is a result of having multiple scavenge sections which pump a lot of air from the engine. If the breather hose is too small, the velocity of the air will increase over what it would be with a larger hose. This increase in velocity will tend to carry more oil droplets to the breather can. This is why a larger hose is better.
Plumbing
AN (Army-Navy) sizes were established by the aircraft industry and designate
the outside diameter of rigid tubing that the corresponding fittings are
used with. Each dash size equals 1/16 of an inch. (ie -8 AN = 8 x 1/16"
= 1/2" OD of the metal tube) Each standard AN size has its own standard
thread size. Since the tube sizes do not equate with the hose sizes, due
to the variation in wall thickness, the ID of the hose and tubes are not
the same.
Oil filters should be located between the oil pump and the oil cooler. Oil pumps create vibrations in the oil which could damage a cooler internally. By having the oil go through the filter first, it removes these vibrations.